Early on in the design, I'd decided I really liked the idea of a Heritage oil-fired cooker/boiler.
I'd seen pictures of boats like Barolo and Quaintrelle which had them fitted and thought they looked lovely.
Not only that, they have some big advantages: they are very compact, being only standard kitchen unit depth and only about 830mm wide, but with an oven big enough to take a large turkey!
The cookers can also go from cold to 200C in 10 minutes or so - not much longer than a domestic gas or electric oven. This is very different to the Aga I grew up with - almost impossible to light and which took forever to get up to a decent cooking temperature!
There are two makes/models of these cookers, identical in all but styling: The Heritage Compact Duette and the Sandyford Cottage. They both have 60,000BTU boilers and twin burners - one for cooking the other for hot water/heating. The slightly scary thing is the price - budget for around £6,500 for a new one!
However, when you offset this against the cost of a 'normal' diesel-fired central heating unit, plus a cooker, plus the gas bottles, etc, it begins to look more attractive. And of course, it meant the possibility of a gas-free boat!
A point of concern was whether the cooker would make the boat too hot in summer, but a conversation with Quaintrelle's owners confirmed 'it's the best thing on the boat!'
Being on a strict budget, I ran routine searches on eBay and other online sites for a second-hand unit. Finally, I struck lucky and found one for sale on eBay (albeit in a rather startling yellow!). I 'sniped' it at the maximum I was prepared to pay and won the auction at £785! Happy days. A specialised transport company moved it very carefully from Kent up to XR&D in Ollerton.
https://www.rangeremoval.com/
I then called in a local specialist to remove the burners, give them a good overhaul and install the necessary diesel pre-heater to convert it from kerosene operation.
Bearing in mind I'd taken a big risk by buying this unseen, I was a bit anxious when I lifted the cover off to take a look. But to be honest, with a good clean, I think it will look fine. The yellow colour is nicer than it appeared in the photos, too. It might be worth getting the top re-enamelled, but otherwise, I think I've got a bargain. Now I just need Lee and Gary to build the boat round it!!
Friday, 30 March 2018
A visit to XR&D
I'd got to the point in the design where it was getting difficult to visualise things. The 'problem' areas were the stern - trying to work out how the swim would affect space and levels and trying to work out the volumes for tanks, etc in the bow.
Luckily, Lee and Gary had a couple of very similar boats in build, at the latter stages of construction. They were happy for me to clamber over them and take lots of measurements and photos.
This shows the well deck of a boat with a Josher bow (mine will be a Trad). Here, we are trying to work out the proportions of the well deck and Potter's locker.
I'd really like the locker to be 100cm front to back a) to make it look right and b) to house the generator lengthways. Otherwise it will take up most of the locker! I also want to leave enough of a well deck to make it a usable space. Thought will also have to be given to side lockers, as the well deck to gunwale will be around 22".
This boat is having a modern engine mounted at quite an oblique angle to allow more room to pass by.
I am proposing more of an S-shaped swim, the idea being to provide an even better flow of water to the prop and improved reversing characteristics.
I did consider a water lubricated stern gland, but I'm concerned about stories of grit causing wear to the shaft and seals.
It might sound silly, but even the dimensions of the roof are important! The distance between the handrails will affect the possible size of solar panels, for instance, whilst still leaving enough room to walk between them.
I'm hoping to fit at least six semi-flexible solar panels to the roof. I know these aren't as efficient as rigid ones, but they are more compact and don't carry the risk of snagging ropes, etc.
My grab rails will be open - basically, lengths of rubbing strake set on studs.
While I was at XR&D, I was able to have a look at a boat being painted in the DIY bay. Interestingly, the roof was being painted in exactly the finish I had identified as probably being the best - Epifane non-slip deck coating.
The red is slightly darker than appears in the photos and is remarkably close to Raddle Red. This was a useful piece of information, as their online colour chart doesn't show this colour!
(I've had those sanded non-slips panels on boats before and have found them terrible dirt traps.)
Luckily, Lee and Gary had a couple of very similar boats in build, at the latter stages of construction. They were happy for me to clamber over them and take lots of measurements and photos.
This shows the well deck of a boat with a Josher bow (mine will be a Trad). Here, we are trying to work out the proportions of the well deck and Potter's locker.
I'd really like the locker to be 100cm front to back a) to make it look right and b) to house the generator lengthways. Otherwise it will take up most of the locker! I also want to leave enough of a well deck to make it a usable space. Thought will also have to be given to side lockers, as the well deck to gunwale will be around 22".
This boat is having a modern engine mounted at quite an oblique angle to allow more room to pass by.
I am proposing more of an S-shaped swim, the idea being to provide an even better flow of water to the prop and improved reversing characteristics.
I did consider a water lubricated stern gland, but I'm concerned about stories of grit causing wear to the shaft and seals.
It might sound silly, but even the dimensions of the roof are important! The distance between the handrails will affect the possible size of solar panels, for instance, whilst still leaving enough room to walk between them.
I'm hoping to fit at least six semi-flexible solar panels to the roof. I know these aren't as efficient as rigid ones, but they are more compact and don't carry the risk of snagging ropes, etc.
My grab rails will be open - basically, lengths of rubbing strake set on studs.
While I was at XR&D, I was able to have a look at a boat being painted in the DIY bay. Interestingly, the roof was being painted in exactly the finish I had identified as probably being the best - Epifane non-slip deck coating.
The red is slightly darker than appears in the photos and is remarkably close to Raddle Red. This was a useful piece of information, as their online colour chart doesn't show this colour!
(I've had those sanded non-slips panels on boats before and have found them terrible dirt traps.)
Sunday, 18 March 2018
Decisions, decisions!
Very often, when people write blogs or produce videos about
a project, they tend to show how they achieved a particular thing, without
really going into all the background thinking and research that went on
beforehand.
A bit like ‘Changing Rooms’, where all the materials used to
magically appear, without the endless and time-consuming visits to B&Q and
HomeBase. Slapping a coat of emulsion on the wall is the easy part. Choosing the
colour from one of a dozen suppliers, the finish, finding the best price and
then actually getting the stuff is the hard part! Not to mention keeping all
the receipts and returning the stuff you don’t need!
The same thing applies to almost every single component and
feature on the boat. To give a simple example: what should the lining be on the
hull sides below the gunwale? The choices could be: horizontal boarding,
vertical boarding or sheet material. You may think this is a decision which
could wait till later in the build, but as with much of this stuff, there are a
lot of dependencies.
Let’s assume we decide on some form of T&G boarding.
Whether it’s vertical or horizontal is going to affect which direction the
supporting battens need to run. So if vertical boarding is chosen, we’re going
to need horizontal battens – one at the top, one at the bottom and a couple in
the middle, to support the board firmly. So we need to fix the battens to
something.
Now take a look at this picture.
The steels run horizontally, but
there are only two of them. So there are two options: either fix vertical
battens on first and then fix horizontal battens to them; or ask the builder to
install the stiffening angles in the vertical. The problem with fixing two
layers of battening is of course, the loss of cabin space. Two extra battens
means 50mm less width!
So having decided to ask the builders to provide vertical
side stiffeners, there is then the question of spacing. Having decided to use
75mm Celotex insulation on the sides, research shows that this comes in 1200mm
x 2400mm sheets – unlike plywood, which is 1220mm x 2440mm. So the angles need
to be set at exactly 605mm centres, to allow a split sheet of insulation to fit
precisely between them without waste.
Back to the subject of the boarding. Next decision: what
material? That decision will be made on preference for appearance, finish
required and cost. The cabin on my boat will be 48’ 6” long – about 14.75m. The
visible height of the side walls will be about 1m. So the area of the two sides
will be just under 30m2. The next task is to work out how many metres of
boarding will be needed; the problem being, most suppliers quote per metre run,
not per square metre. Not helped by the fact that T&G is often quoted as,
for instance, ‘Ex 19mm x 100mm’.
In other words, the T&G shape is produced
from that section of timber, but the finished size will be a lot less. In the example shown, 11mm width is lost in the machining process. The
thickness is fairly important, but the effective width really matters. With
about 200 strips to be installed down each side, a few millimetres more or less
will make a big difference! Frustratingly, very few suppliers quote the
coverage width, so it really needs an enquiry or a sample. The example above does not give the effective width, so the dimnsion for the tongue needs to be deducted, giving an actual width of about 83mm.
Let’s assume by this stage, we have decided to use softwood
T&G. An important consideration is the
thickness of the boards. ‘T&G cladding’ from B&Q might look like a
cheap solution, but will it be thick enough to not flex? What is the quality
like? Will you lose large amounts due to waste? Will the standard lengths result
in hundreds of wasteful off-cuts?
It may be that a board from another supplier, whilst more
expensive per linear metre, might be a better bargain, if it provides a greater
coverage width, is of better quality and results in less waste.
![]() |
I like this style! |
Then there’s the question of the surface finish… paint or
varnish? What colour? What finish?
I’ve gone through this process in detail, just to show that
even for an apparently really simple and straightforward task, like the lining
of the hull sides, there's actually a great deal of thought and research
required, particularly if costly mistakes are to be avoided.
I am working to a very tight budget for the ‘Calbourne’
build, so any money that can be saved in one area provides leeway in another.
The remarkable thing is the sheer variance in price for an identical item from
different suppliers. For example, I have pretty well decided on the Hyundai
DHY6000SE diesel generator. I have seen this advertised at a range of prices
from £1,720 to £1,193 – a difference of £527 for precisely the same item.
Shopping around definitely pays!
This principle applies to even the most mundane of tems. Take the ballast for example. Again, there are numerous options, even after working out how much is needed. Steel offcuts are far heavier than concrete, but expensive; concrete bricks and slabs of various sizes are all contenders. The lowest cost per kilo are 'council' paving slabs - 600 x 900, weighing in at 60-odd Kg each. But that low cost needs to be offset against the back-breaking job of getting them into the boat and laying them. Other options include 600 x 600 slabs and concrete bricks weighing 3Kg each. If we go for the slabs, do they need to be one or two layers thick? If the bricks, do they need to be laid flat or on edge? The answers to those questions determines the height of the floor above the baseplate... which governs the arrangement of battening to be fixed to the steel bearers...
And so the seemingly endless iterations and calculations go on!
I now have a spreadsheet which runs to over 150 lines, which
shows all the main items and components required for the build. In every case,
I have identified the item, supplier, price and quantity required. This is the
result of over 9 months’ spare time research, but has resulted in savings of thousands
from the original estimate. It has been an informative and productive use of time
during a period when no ‘hands on’ work could be done. This ‘hiatus’ time has
also allowed early ideas and assertions to be questioned and either verified or
discarded, so has certainly not been wasted. I’m hoping that by the time I
start the actual work, I'm hoping I'll know exactly what I need, where I’ll be getting
it from and how much it will cost!
Saturday, 17 March 2018
Underfloor heating
In an earlier post, I mentioned my wish to have underfloor heating - or UFH.
UFH can be either a web of electric heating elements or a series of pipes filled with water. Electric is impractical on a boat, but wet UFH can be heated with any normal heat source. The vital thing is that the pipes are set into highly insulating boards, to prevent heat loss on the wrong side. Quality insulating panels also have a metal layer on the top surface, to help spread the heat.
There were a number of reasons why I liked the idea of UFH. Having already committed to the idea of a central heating cooking range, I would have ample hot water. I didn’t really want the coal storage, dust and ash disposal issues of a solid fuel fire. Most particularly, I didn’t want the ‘roasting saloon/freezing bedroom’ problem, so often encountered. Plus, we don’t like our dogs roasting themselves in front of a fire. It’s not good for them, but hard to prevent. Another perennial problem is heating the bathroom. The ‘smallest room’ has the least space to install a radiator, but really needs the most heat! Finally, I find that radiators take up quite a lot of room and can be knee-cracking annoyances. UFH could address all these points.

However, an issue which was identified quite early on, was the resulting thickness of the floor. In order to prevent heat being lost to the bilge, a high quality insulation layer is needed. So on top of the normal 18mm ply floor would be a 25mm insulating/pipe layer, with another 18mm engineered oak layer on top of that. So it looked like the headroom would be reduced by 43mm, compared to a standard ply floor. I didn’t relish the idea of losing nearly 2” of headroom.
I came up with a novel solution to overcome this problem. Normally, the 100cm sheets of steel used to form the cabin side are taken up beyond the roofline to form the handrail, which is about 40mm
high. But by using the whole of the sheet width as the cabin side, it would be possible to very nearly regain the lost headroom. The handrail would then be formed from D-section (rubbing strake) steel mounted on studs to form a ‘rat-trap’ rail. In my view, this brings other benefits, such as not trapping dirty water and allowing rainwater to run off along the boat, rather than being channelled in one small area. The guys at XR&D agreed that the slightly higher cabin side wouldn't upset the balance of the boat design. Tick.
One of the main reasons people don’t adopt UFH on narrowboats, is the lack of exposed floor area, because much of it is covered by cupboards and other furniture. Fair point – UFH is a low grade heat which requires a large radiating area. However, I could also see a benefit in having, for example, the under bed storage being gently warmed.
I pondered this problem for quite a while, then had a lightbulb moment. Why only use UFH under the floor? The boat sides are about a metre high. The two sides equal the width of the floor and are largely, more exposed. So why not continue the UFH insulating boards and pipework up the sides? A call to a UFH specialist company confirmed that they could see no reason why it wouldn’t work, as long as there was a good air removal device in the system.
The idea worked in well. The vertical side bearers are 50mm deep, so this space will be filled by 50mm Celotex. On top of the bearers will be three 25mm longitudinal battens. Between the battens will be two 415mm strips of 25mm UFH insulation panel. Each strip will be able to house three runs of pipe at 150mm centres. I am even considering running UFH pipes through the bulkhead behind the shower to provide additional warmth.
This arrangement should result in a U-section of gentle radiated warmth, extending the length of the cabin. I anticipate that this will provide a comfortable environment, which will be controlled by a thermostat.
Ballast. There is also another issue, frequently not commented upon. Given the construction sequence: ballast, battening, plywood, insulation, pipework, finish floor, furniture and fittings, the slightly scary realisation was that the ballast, once in, will be inaccessible. This meant that very accurate calculations would be needed to ensure that ballast will be located in the right quantity and location – fore/aft and left/right!
In order to try to get the ballasting of the boat right, I am working with a spreadsheet which takes into account the total weight of an item and how far left or right of the centreline it will be located. So for example, the cooking range weighs around 400Kg. Its centre will be 300mm from the left side, roughly two thirds of the distance from the centreline. So the effective weight being applied to the left side of the boat is 266Kg. By repeating this exercise for all of the significant items, I should be able to get within the realms of correctable ballasting. In practical terms, this means shifting some 56lb weights around!
The design of the UFH system should result in about 40m2 of UFH area, of which about 60% will be exposed. Given the high insulation value of the boat - even the cabin sides and roof will have 50mm Celotex - this should be very adequate and result in cosy warm floors.
Back up. In recognition of the fact that I will have a lot of eggs in one basket, I also plan to install a small multifuel stove, just for emergencies or effect when required. This will help to counter the problem of a complete failure of say, the burner unit in the cooker.
Cost. The installation of UFH is not a particularly costly exercise and is very comparable with the cost of decent quality radiators, pipework and valves.
UFH can be either a web of electric heating elements or a series of pipes filled with water. Electric is impractical on a boat, but wet UFH can be heated with any normal heat source. The vital thing is that the pipes are set into highly insulating boards, to prevent heat loss on the wrong side. Quality insulating panels also have a metal layer on the top surface, to help spread the heat.
There were a number of reasons why I liked the idea of UFH. Having already committed to the idea of a central heating cooking range, I would have ample hot water. I didn’t really want the coal storage, dust and ash disposal issues of a solid fuel fire. Most particularly, I didn’t want the ‘roasting saloon/freezing bedroom’ problem, so often encountered. Plus, we don’t like our dogs roasting themselves in front of a fire. It’s not good for them, but hard to prevent. Another perennial problem is heating the bathroom. The ‘smallest room’ has the least space to install a radiator, but really needs the most heat! Finally, I find that radiators take up quite a lot of room and can be knee-cracking annoyances. UFH could address all these points.

However, an issue which was identified quite early on, was the resulting thickness of the floor. In order to prevent heat being lost to the bilge, a high quality insulation layer is needed. So on top of the normal 18mm ply floor would be a 25mm insulating/pipe layer, with another 18mm engineered oak layer on top of that. So it looked like the headroom would be reduced by 43mm, compared to a standard ply floor. I didn’t relish the idea of losing nearly 2” of headroom.
I came up with a novel solution to overcome this problem. Normally, the 100cm sheets of steel used to form the cabin side are taken up beyond the roofline to form the handrail, which is about 40mm
high. But by using the whole of the sheet width as the cabin side, it would be possible to very nearly regain the lost headroom. The handrail would then be formed from D-section (rubbing strake) steel mounted on studs to form a ‘rat-trap’ rail. In my view, this brings other benefits, such as not trapping dirty water and allowing rainwater to run off along the boat, rather than being channelled in one small area. The guys at XR&D agreed that the slightly higher cabin side wouldn't upset the balance of the boat design. Tick.
One of the main reasons people don’t adopt UFH on narrowboats, is the lack of exposed floor area, because much of it is covered by cupboards and other furniture. Fair point – UFH is a low grade heat which requires a large radiating area. However, I could also see a benefit in having, for example, the under bed storage being gently warmed.
I pondered this problem for quite a while, then had a lightbulb moment. Why only use UFH under the floor? The boat sides are about a metre high. The two sides equal the width of the floor and are largely, more exposed. So why not continue the UFH insulating boards and pipework up the sides? A call to a UFH specialist company confirmed that they could see no reason why it wouldn’t work, as long as there was a good air removal device in the system.
The idea worked in well. The vertical side bearers are 50mm deep, so this space will be filled by 50mm Celotex. On top of the bearers will be three 25mm longitudinal battens. Between the battens will be two 415mm strips of 25mm UFH insulation panel. Each strip will be able to house three runs of pipe at 150mm centres. I am even considering running UFH pipes through the bulkhead behind the shower to provide additional warmth.
This arrangement should result in a U-section of gentle radiated warmth, extending the length of the cabin. I anticipate that this will provide a comfortable environment, which will be controlled by a thermostat.
Ballast. There is also another issue, frequently not commented upon. Given the construction sequence: ballast, battening, plywood, insulation, pipework, finish floor, furniture and fittings, the slightly scary realisation was that the ballast, once in, will be inaccessible. This meant that very accurate calculations would be needed to ensure that ballast will be located in the right quantity and location – fore/aft and left/right!
In order to try to get the ballasting of the boat right, I am working with a spreadsheet which takes into account the total weight of an item and how far left or right of the centreline it will be located. So for example, the cooking range weighs around 400Kg. Its centre will be 300mm from the left side, roughly two thirds of the distance from the centreline. So the effective weight being applied to the left side of the boat is 266Kg. By repeating this exercise for all of the significant items, I should be able to get within the realms of correctable ballasting. In practical terms, this means shifting some 56lb weights around!
The design of the UFH system should result in about 40m2 of UFH area, of which about 60% will be exposed. Given the high insulation value of the boat - even the cabin sides and roof will have 50mm Celotex - this should be very adequate and result in cosy warm floors.
Back up. In recognition of the fact that I will have a lot of eggs in one basket, I also plan to install a small multifuel stove, just for emergencies or effect when required. This will help to counter the problem of a complete failure of say, the burner unit in the cooker.
Cost. The installation of UFH is not a particularly costly exercise and is very comparable with the cost of decent quality radiators, pipework and valves.
Subscribe to:
Posts (Atom)
Maiden voyage and cooker!
It's been an eventful few days! We've been enjoying a spell of unseasonably warm weather, which was predicted to end on the last day...
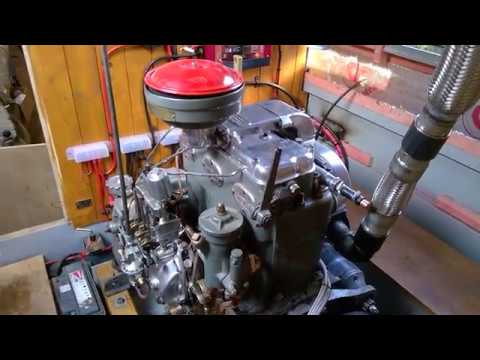
-
Early on in the design, I'd decided I really liked the idea of a Heritage oil-fired cooker/boiler. I'd seen pictures of boats like ...
-
I had originally thought to use cable controls with a 'Morse' type lever. But the practicality of trying to mate these cables to a v...
-
Just to recap a bit on previous posts... One of the main reasons given for not installing 'wet' underfloor heating in a boat, is t...